top of page

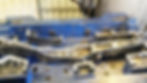
QUALITY CONTROL SYSTEM & METHOD IN THE PROCESS OF SHAPING WITH DEEP DRAWING
DUE TO SEVERAL REASONS, THE MATERIAL DOES NOT FLOW IN THROUGH DIE AND TEARS DURING THE FORMATION OF METAL MATERIAL; IT IS CALLED AS 'CRACK'.
UNTIL THIS FORMED CRACK WILL BE DETECTED BY QUALITY OPERATOR, MINIMUM 9 PANELS WOULD BE CRACKED.
SOMETIMES, THE CRACKS IN HARDLY VISIBLE REGIONS WILL NOT BE SEEN AND ALL THE PANELS COULD BE SCRAP.

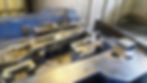
ARTIFICIAL SEEING SYSTEM WITH CAM
INTERNATIONALLY PATENTED
THE FIRST & UNIQUE IN THE WORLD
OUR PRODUCT IS A SYSTEM WHICH DETECTS DEFAULT PRODUCTION PANEL AND STOPS THE LINE
“QUALITY CONTROL SYSTEM AND METHOD IN THE PROCESS OF SHAPING WITH DEEP DRAWING”
IS AN INTERNATIONALLY PATENTED TECHNOLOGY PRODUCT.
THIS SYSTEM CAN BE SOLD TO HUNDREDS OF LOCAL AND INTERNATIONAL COMPANIES.
BESIDE HUGE BENEFITS TO COUNTRY'S ECONOMY, IT PROVIDES BETTER PRODUCT QUALITY,
SAVING AND COST CONTRIBUTION, WHICH ACHIEVES MORE VALUE THAN ITS PERFORMANCE.
CRACK
-
CRACK PROBLEM IS AN IMPORTANT QUALITY FAULT.
-
IT IS NOT POSSIBLE TO REPAIR.
-
IT IS FULLY SCRAPPED.
-
IT IS NOT SAFE TO USE, IT AFFECTS THE RESISTANCE OF THE PRODUCT.
-
THE DETECTION OF THE CRACK AND DIE REPAIR CAUSE LONG TERM STOPS IN THE PRESS LINE.
-
IT CAUSES NOT TO COMPLETE OPERATION IN PLANNED TIME.
-
THE EFFICIENCY OF THE LINE DROPS DOWN.
-
IT INCREASES THE RISK TO BE DAMAGED, WHILE ENTERING TO THE LINE DURING EVERY INTERVAL AND MAY CAUSE HIGH DANGER TO BE STUCK BY THE MACHINE.
-
DURING THE SCANNING OF FAULTED PRODUCT, IT INCREASES THE RISK TO HANDLE ALL PRODUCTS ONCE MORE AND MAY CAUSE TO BE CUT.
-
THE TRANSPORT AND DISPOSAL OF FAULTED PRODUCTS CAUSE NEW RISKS TO WORK SECURITY.
-
STOCK CONTROLS MADE OUT OF THE LINE MAY CAUSE ERGONOMIC RISKS.
​
METHOD AND PROCESSING OF THE SYSTEM:
-
SIDE DETECTION ALGORITHM
-
CORRECTION OF PERSPECTIVE
-
HOMOGENEOUS COORDINATES
-
GAUSS JORDAN METHODS.
​
RETURN OF THE SYSTEM:
-
THE POSSIBILITY OF VERY FAST CONTROL WHICH CAN NOT BE DONE BY HUMAN EYE.
-
THE POSSIBILITY OF MILIMETRIC SENSITIVITY CONTROL.
-
AUTOMATIC DETECTION OF FAULTED PRODUCTS.
-
IT PREVENTS TO SEND FAULTED PRODUCT TO SECOND PROCESS STEP AND PREVENTS DIE TO BE DAMAGED.
-
IT ESTABLISHES A CONTROL MECHANISM WHICH IS FULLY INDEPENDENT FROM OPERATOR, TIME, PERSON;
SO PROVIDES QUALITY CONTROL.
-
IT PROVIDES TO PRODUCE BY 99,15% PRECISION QUALITY.
bottom of page